Introduction
Work trucks are essential vehicles used in various industries for transporting goods, equipment, and personnel. These vehicles play a crucial role in the efficiency and productivity of businesses. However, operating work trucks can be hazardous, especially when proper safety precautions are not taken. To mitigate risks and ensure the safety of drivers, passengers, and pedestrians, it is essential to equip work trucks with the necessary safety equipment. In this comprehensive guide, we will explore the importance of work truck safety equipment, the different types of safety gear available, and best practices for maintaining a safe work environment.
The Importance of Work Truck Safety Equipment
Work truck safety equipment is designed to protect drivers, passengers, and pedestrians from accidents and injuries. By equipping work trucks with the appropriate safety gear, businesses can minimize the risks associated with operating these vehicles and create a safer work environment for everyone involved. Some of the key reasons why work truck safety equipment is essential include:
1. Preventing Accidents: Work trucks are often large and heavy vehicles that can be challenging to maneuver, especially in busy worksites or on crowded roads. Safety equipment such as backup cameras, blind spot monitors, and proximity sensors can help drivers avoid accidents by providing them with better visibility and awareness of their surroundings.
2. Protecting Personnel: Work trucks are commonly used to transport personnel to and from job sites. In the event of a collision or rollover, safety equipment such as seat belts, airbags, and roll bars can help protect passengers from serious injuries or fatalities.
3. Enhancing Vehicle Stability: Work trucks are susceptible to rollovers, especially when carrying heavy loads or navigating uneven terrain. Safety equipment such as stability control systems, anti-lock brakes, and tire pressure monitoring systems can help improve the stability and handling of work trucks, reducing the risk of rollover accidents.
4. Compliance with Regulations: Many jurisdictions have regulations and standards in place that require work trucks to be equipped with specific safety equipment. By ensuring compliance with these regulations, businesses can avoid fines, penalties, and legal liabilities.
Types of Work Truck Safety Equipment
There are various types of safety equipment available for work trucks, each serving a specific purpose in enhancing the safety of the vehicle and its occupants. Some of the most common types of work truck safety equipment include:
1. Seat Belts: Seat belts are one of the most basic yet essential safety features in any vehicle, including work trucks. Garbage truck waste handling help restrain occupants in the event of a collision or sudden stop, reducing the risk of injuries.
2. Airbags: Airbags are designed to deploy in the event of a collision to provide an additional layer of protection for occupants. Most modern work trucks are equipped with front airbags for the driver and front passenger, as well as side curtain airbags for added safety.
3. Anti-lock Braking System (ABS): ABS helps prevent the wheels from locking up during emergency braking, allowing the driver to maintain steering control and avoid skidding. ABS is particularly useful in slippery conditions or when stopping suddenly.
4. Stability Control Systems: Stability control systems help prevent rollovers and loss of control by applying brakes to individual wheels and adjusting engine power as needed. These systems are especially beneficial for work trucks carrying heavy loads or operating on uneven terrain.
5. Backup Cameras: Backup cameras provide drivers with a clear view of the area behind the truck when reversing, helping them avoid obstacles, pedestrians, and other vehicles. Backup cameras are particularly useful in tight spaces or congested areas.
6. Blind Spot Monitors: Blind spot monitors use sensors to detect vehicles or objects in the truck's blind spots and alert the driver through visual or audible warnings. These systems help prevent accidents caused by lane-changing or merging maneuvers.
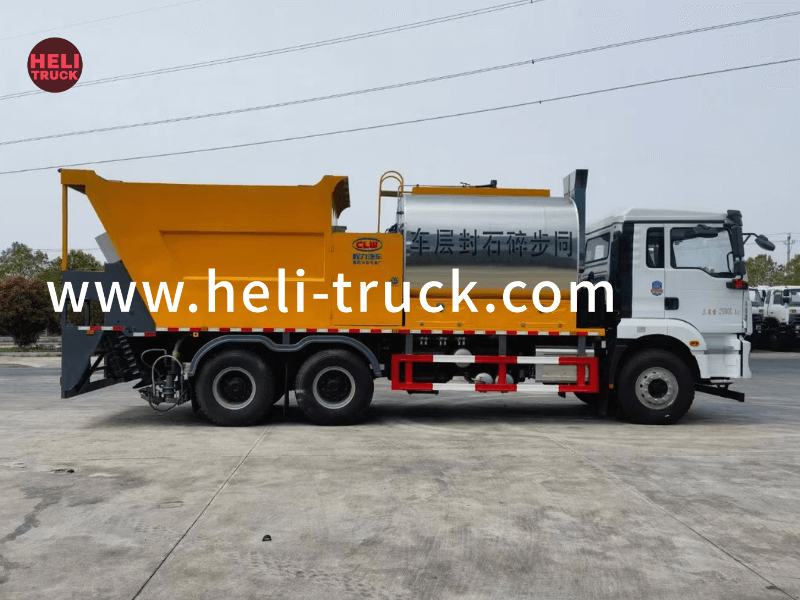
7. Proximity Sensors: Proximity sensors alert drivers to obstacles or pedestrians in close proximity to the truck, helping prevent collisions during parking or maneuvering. Proximity sensors are especially useful in crowded worksites or urban environments.
8. Roll Bars: Roll bars are structural components installed in the truck's cabin to provide protection in the event of a rollover accident. Roll bars help prevent the roof from collapsing and protect occupants from serious injuries.
9. Fire Extinguishers: Fire extinguishers are essential safety equipment in case of a fire emergency. Work trucks should be equipped with a properly maintained fire extinguisher to quickly respond to and contain fires.
10. Emergency Exit Tools: In the event of a crash or rollover that compromises the doors or windows, emergency exit tools such as window breakers and seatbelt cutters can help occupants escape the vehicle quickly and safely.
Maintaining Work Truck Safety Equipment
Ensuring the effectiveness of work truck safety equipment requires regular maintenance, inspection, and testing. Businesses should establish a comprehensive maintenance program to keep safety equipment in optimal condition and address any issues promptly. Some best practices for maintaining work truck safety equipment include:
1. Regular Inspections: Conduct regular inspections of safety equipment, including seat belts, airbags, brakes, and stability control systems, to check for signs of wear, damage, or malfunction. Replace any faulty components immediately.
2. Testing and Calibration: Test safety equipment such as ABS, stability control systems, backup cameras, and proximity sensors regularly to ensure they are functioning correctly. Calibration may be necessary to maintain accuracy and reliability.
3. Proper Installation: Ensure that safety equipment is installed correctly and securely to prevent malfunctions or failures during operation. Follow manufacturer guidelines and specifications for installation procedures.
4. Training and Education: Provide drivers and personnel with training on how to use and maintain safety equipment properly. Educate them on the importance of safety precautions and best practices for preventing accidents.
5. Emergency Response Planning: Develop and communicate emergency response plans that outline procedures for responding to accidents, fires, or other emergencies involving work trucks. Ensure that all occupants are familiar with emergency exits and tools.
6. Record-Keeping: Maintain detailed records of safety equipment inspections, maintenance activities, repairs, and replacements. Documentation can help track the condition of safety equipment and ensure compliance with regulations.
Conclusion
Work truck safety equipment plays a critical role in protecting drivers, passengers, and pedestrians from accidents and injuries. By equipping work trucks with the necessary safety gear, businesses can enhance the safety of their operations, comply with regulations, and mitigate risks associated with operating these vehicles. From seat belts and airbags to stability control systems and emergency exit tools, there are various types of safety equipment available to improve the safety of work trucks. By implementing regular maintenance practices, training programs, and emergency response planning, businesses can ensure that their work trucks are equipped to operate safely in various environments. Prioritizing work truck safety is not only a legal requirement but also a moral obligation to protect the well-being of everyone involved in the operation of these essential vehicles.